Area Dust Control
The main theory behind Dust Suppression is that when a water droplet comes in contact with a dust particle, it will agglomerate, and the resulting combination will be too heavy to remain suspended. The water droplet/dust particle combination will fall where the dust can be disposed of.
The most effective dust removal can be obtained if droplets should typically be 1 to 5 times the size of the dust that is being controlled. If the drops are too small, they will be unable to agglomerate with and knock down the dust particles. Conversely, water drops that are significantly larger than the dust particles form an air barrier around themselves, preventing the dust from gaining direct contact and encapsulation/agglomeration with the water droplet.
BETE can provide droplet size distributions to aid in the selection of the correct nozzle and operating parameters
Conveyor and Transfer Point Dust Control
The movement of conveying crushed stone, coal, or sand stirs up and creates a dust cloud, which can be suppressed by spraying water as a fine mist or fog. Adding finely sprayed water to the minerals or aggregates on conveyors or at transfer points and hoppers can prevent dust generation or suppress created dust clouds and keep them from spreading. The sprayed water can prevent the dust cloud from forming by adhering the dust to the mineral being processed or agglomerated with the air’s dust particles. Effective dust control on conveyors and transfer points can also play a critical role in preventing dust explosions and be a key safety system in processing plants and power generation facilities.
For preventative dust control to be effective, coverage and distribution are essential. Ensuring complete coverage of the material being transferred ensures proper wetting of all the material and prevents dust formation. However, over-spray can waste resources and build-up on other portions of transfer equipment. In many applications, surfactants or foaming chemicals are added to help the sprayed water effectively cover and penetrate material transferred on a conveyor.
Common Uses & Industries 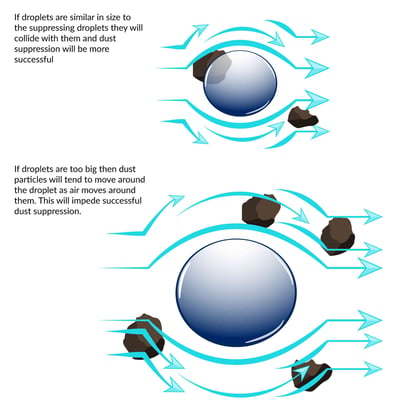
- Mining
- Loading hoppers
- Rock crushers
- Corn, wheat, and grain processing
- Waste Management Industry
___________________________________________________________________________
Important factors to Consider When Selecting a BETE Dust Control Nozzle:
- Prevention vs suppression water spray systems
- Dust particle size and concentration
- Amount of raw material and conveyors speeds
- Required coverage
- Available nozzle mounting locations
- Available and allowable water flow rates
- Sufficient water to effectively prevent or suppress dust is required, but too much water addition can create binding or clogging of downstream equipment, affecting the transport costs of materials, or affecting the BTU content of coal, among other factors
- Available liquid pressure drop (∆P) across the nozzle(s)
∆P - supply pressure at nozzles inlet - process pressure outside nozzle